
Réduire le coût de développement des avions de chasse grâce à une conception adaptée, des outils numériques et des coopérations ciblées.
Le développement des avions de chasse est connu pour son coût de développement élevé. Cela recouvre la conception des avions de chasse, l’élaboration de prototypes, la réalisation d’essais, puis l’industrialisation. Des programmes récents, tels que le F-35 ou le Rafale, ont montré que le développement des avions de chasse pouvait facilement atteindre plusieurs dizaines de milliards d’euros. Ces montants proviennent de la complexité technique, du niveau d’intégration de multiples systèmes avancés, ainsi que des nombreuses contraintes réglementaires et opérationnelles.
La question de réduire ce coût de développement apparaît désormais centrale. Les responsables cherchent des méthodes claires et concrètes afin de mieux maîtriser l’ensemble du processus. Les objectifs incluent une diminution du temps consacré aux phases d’essais, une amélioration de la robustesse dès la conception, et une rationalisation des composants et des matériaux. Des approches existent déjà, comme l’utilisation d’outils numériques, le recours à des simulations plus complètes, ou encore une standardisation accrue de certaines pièces. Des accords industriels plus larges, une répartition plus équilibrée des charges, ou l’adoption de nouvelles méthodes d’approvisionnement s’imposent également.
Le but est d’obtenir un équilibre durable entre performance, qualité et maîtrise budgétaire. Le développement des avions de chasse doit s’appuyer sur des approches plus sobres, sans compromettre les exigences opérationnelles. Les secteurs impliqués s’interrogent sur la meilleure façon de procéder, tout en tenant compte de contraintes externes, comme les rythmes d’évolution technologique, la pression concurrentielle, ou les politiques de défense. Des pistes multiples existent, ouvrant la voie à une refonte des pratiques.
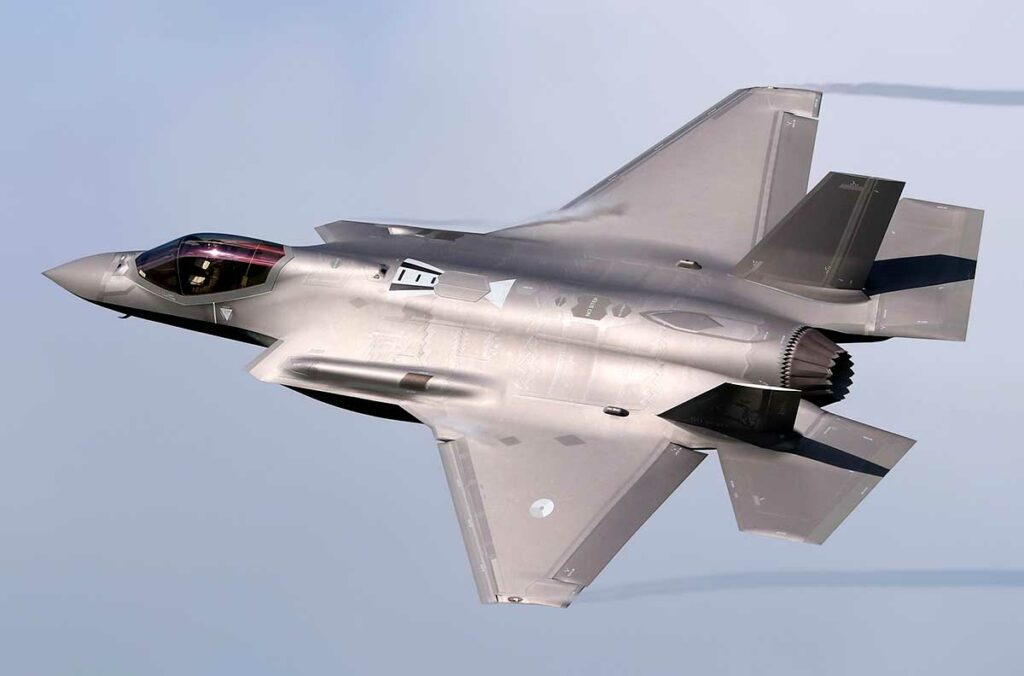
Contexte du coût de développement dans la conception des avions de chasse
Analyse des montants investis
Le coût de développement d’un avion de chasse atteint souvent plusieurs dizaines de milliards EUR. Le programme F-35, initié par Lockheed Martin, illustre ce phénomène. Selon diverses estimations, le développement initial, incluant recherche et prototypage, a dépassé 50 milliards EUR. Le programme Rafale, conçu par Dassault Aviation, affiche aussi un niveau budgétaire similaire sur la phase de conception et d’ingénierie. Ces montants couvrent l’intégration d’équipements complexes, les essais en vol, la certification et l’industrialisation progressive.
Exigences réglementaires et opérationnelles
Le respect des normes internationales et l’obtention des certifications imposent une série d’essais et de validations. Chaque exigence ajoutée allonge le calendrier et accroît la facture totale. Par exemple, l’intégration d’un radar AESA (Active Electronically Scanned Array) nécessite un test minutieux, incluant évaluation des performances dans diverses conditions atmosphériques. L’incorporation de matériaux composites, plus légers que l’acier, impose également des validations spécifiques. Chaque contrainte réglementaire ou opérationnelle exige une revue technique, un ajustement et un contrôle étendu.
Pression concurrentielle et enjeux stratégiques
La conception d’un avion de chasse se déroule dans un contexte concurrentiel, avec des acteurs cherchant à acquérir un avantage technologique. Cette compétition incite à intégrer des systèmes d’armes avancés, des systèmes de communication cryptés et des capteurs adaptatifs. Le dépassement des objectifs initiaux arrive fréquemment lorsque des fonctionnalités supplémentaires s’ajoutent en cours de route, créant des besoins de réingénierie et de nouvelles campagnes d’essais. Cette dynamique accroît le coût global et incite chaque acteur à surveiller de près les choix technologiques, les contrats de sous-traitance et le calendrier.
Rationalisation des processus de R&D
Réduction des phases d’essais réels grâce à la simulation
La simulation numérique permet de limiter le nombre d’essais en conditions réelles. Des logiciels tels qu’Ansys ou Siemens Simcenter évaluent la portance, la traînée ou la stabilité aérodynamique. Cette approche diminue le recours aux prototypes coûteux. Par exemple, simuler le comportement d’un matériau composite spécifique réduit la nécessité de fabriquer plusieurs pièces pour valider ses propriétés. De plus, ajuster un profil aérodynamique sur un modèle virtuel permet de vérifier le comportement à différentes vitesses, entre 0 et 2 000 km/h, sans engager de longues campagnes d’essais en vol. Cette méthode génère un gain financier important, souvent estimé à plusieurs centaines de millions EUR.
Amélioration de la robustesse dès la phase de conception
Intégrer des outils de calcul par éléments finis (FEA) et de conception assistée par ordinateur (CAO) dès les premières étapes permet d’anticiper les contraintes structurelles. Les ingénieurs vérifient la résistance des ailes en simulant des charges de plusieurs dizaines de kN. Ils affinent ainsi la répartition des efforts sur la structure, ce qui réduit les corrections ultérieures. Cette démarche limite les interventions sur les prototypes physiques et diminue le temps total de mise au point.
Optimisation du cycle de vie des composants
Analyser la durée de vie prévisionnelle des pièces dès la conception assure une meilleure prévision du coût global. Des données sur la résistance à la fatigue, la corrosion, ou l’usure des éléments critiques servent à choisir des alliages spécifiques et à établir un calendrier d’inspections optimisé. Une simple adaptation du matériau d’un roulement, affichant une durée de vie prolongée de 20 %, limite le besoin de remplacement sur le long terme. Cette approche réduit la facture de maintenance et assure un suivi budgétaire plus précis sur toute la durée d’exploitation.
Standardisation et modularité des pièces
Adoption de composants interchangeables
L’adoption de composants standardisés favorise la réutilisation sur différents modèles. Par exemple, un système hydraulique générique s’installe sur plusieurs versions d’un appareil. Cette pratique diminue les coûts de développement, car un seul processus de conception et de validation suffit. Un réservoir de carburant conçu pour un modèle peut s’adapter, par quelques ajustements, à un autre, sans engager un nouveau cycle de R&D complet. Cette méthode limite la fabrication de pièces spécifiques, souvent plus coûteuses, et réduit le temps de conception total.
Simplification de la maintenance et de la logistique
Des composants modulaires facilitent la maintenance, car l’atelier peut remplacer rapidement une pièce sans devoir stocker une grande quantité de pièces différentes. Une unité électronique standard évite l’acquisition d’un stock important. Cette simplification améliore la disponibilité et la fiabilité, tout en limitant les coûts d’entreposage. Par exemple, un module électronique universel coûte environ 100 000 EUR, alors qu’un équivalent spécifique, conçu uniquement pour un modèle particulier, peut atteindre plus de 200 000 EUR.
Réduction de la dépendance à des fournisseurs spécifiques
L’emploi de matériels interchangeables diminue la dépendance vis-à-vis d’un fournisseur unique. Cette flexibilité permet de négocier les tarifs et les délais de livraison. Un composant générique, produit par plusieurs industriels, offre des tarifs plus bas qu’une pièce exclusive. Par exemple, un servo-moteur générique, disponible chez plusieurs fournisseurs, peut coûter environ 50 000 EUR, contre plus de 80 000 EUR pour un équivalent exclusif. Cette approche soutient une maîtrise budgétaire et sécurise l’approvisionnement.
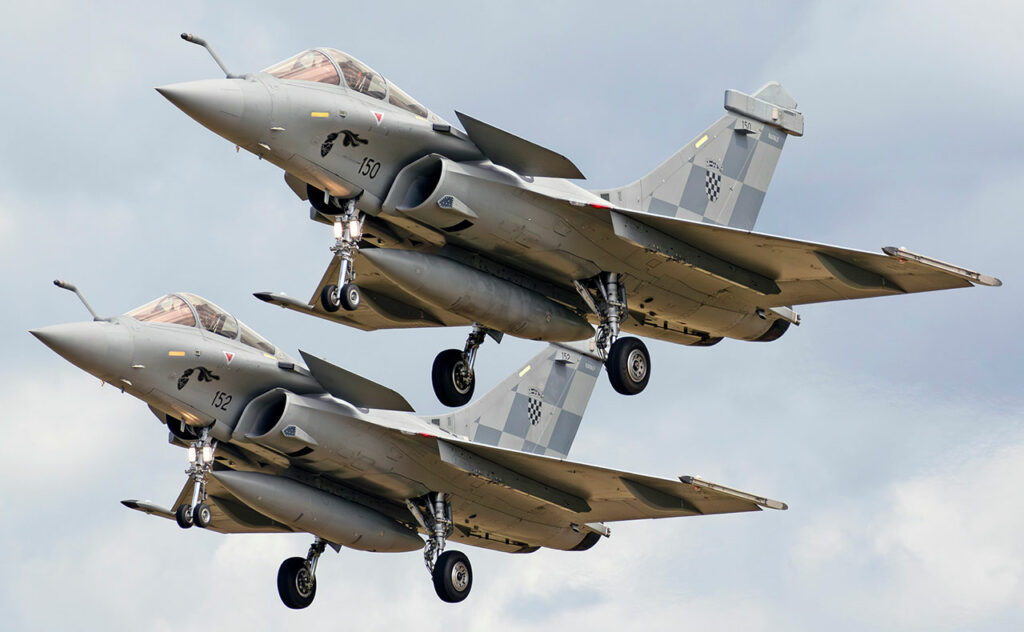
Outils numériques et ingénierie virtuelle
Simulation des performances en amont
L’usage de logiciels de simulation tels qu’ANSYS ou Dassault Systèmes SIMULIA facilite la prédiction des charges, de la résistance des matériaux, et de l’aérodynamique avant la production. Simuler le flux d’air à 2 000 km/h permet d’ajuster le profil d’une aile sans créer de prototype physique. Cette pratique, facturée souvent autour de 500 000 EUR pour une série d’analyses, peut éviter plusieurs millions EUR de dépenses liées à des essais réels en soufflerie. Cette approche réduit aussi la durée des campagnes de test sur site et limite les modifications tardives.
Prototypage virtuel et maquettes numériques
Les outils de modélisation 3D offrent la possibilité de constituer un modèle complet dans un environnement virtuel. Cette représentation présente la géométrie, l’agencement interne et les interfaces entre divers systèmes. Un ingénieur peut, par exemple, vérifier l’emplacement d’un réservoir de 500 L et repérer une contrainte de montage à un stade précoce. Cette méthode limite la création de prototypes physiques, dont le coût peut atteindre plusieurs dizaines de millions EUR. En détectant les erreurs plus tôt, elle évite des corrections ultérieures complexes.
Gestion intégrée des données techniques
Les systèmes PDM (Product Data Management) ou PLM (Product Lifecycle Management) centralisent l’ensemble des données relatives aux conceptions. Les plans, modèles 3D, spécifications et configurations restent accessibles sur une plateforme unique. Cette intégration simplifie la coordination entre les équipes, réduit les incohérences et prévient les achats inutiles. Un capteur à 30 000 EUR peut ainsi être identifié rapidement, évitant des commandes superflues. Les données techniques organisées de façon cohérente diminuent les pertes de temps et les modifications redondantes.
Partenariats industriels et coopérations internationales
Répartition des coûts entre plusieurs acteurs
Un programme impliquant plusieurs participants permet de répartir la charge financière sur plusieurs budgets nationaux ou industriels. Par exemple, le programme Eurofighter Typhoon, partagé entre le Royaume-Uni, l’Allemagne, l’Italie et l’Espagne, a permis de mutualiser des investissements estimés à plus de 50 milliards EUR. Cette approche limite la dépendance d’un acteur unique et diminue le coût unitaire par appareil. La répartition des efforts de R&D, des essais en vol et de la production évite de supporter seul la totalité des dépenses.
Transferts de savoir-faire et consolidation des compétences
Un partenariat international facilite l’échange de connaissances et de méthodes. Un acteur maîtrisant l’aérodynamique collabore avec un autre spécialisé dans l’électronique de bord. Cette interaction accélère le développement, car chaque équipe évite d’investir des années dans l’acquisition de compétences déjà présentes ailleurs. Par exemple, un centre de recherche français collaborant avec un laboratoire allemand réduit le temps dédié à la mise au point d’un radar à antenne active. Le partage des données de test, l’accès à des technologies déjà éprouvées et l’optimisation de la formation interne abaissent les risques d’erreurs et de retards.
Accords favorisant les synergies techniques
Des accords formels entre acteurs définissent les rôles et les responsabilités, ainsi que les calendriers. Un contrat clair, un plan de travail cohérent et des jalons techniques précis assurent une organisation efficace. Par exemple, un groupe défini pour la propulsion, un autre pour le fuselage et un troisième pour l’avionique. Cette segmentation rationnelle limite les redondances et réduit le risque de coûts supplémentaires. L’objectif est de rendre chaque sous-système compatible, de limiter les retouches et de valider les performances dans un délai maîtrisé. Cette méthode permet de stabiliser le budget global et d’aboutir plus rapidement à un appareil conforme aux exigences opérationnelles.
Approvisionnement, supply chain et contrôle des coûts
Sélection rigoureuse des fournisseurs
Une analyse précise des fournisseurs assure une qualité constante et des délais maîtrisés. Par exemple, l’utilisation d’un seul partenaire spécialisé dans la fabrication d’éléments en alliage léger, facturés environ 200 000 EUR par lot de 10 pièces, réduit le risque de défauts. Cette stratégie offre une stabilité sur la durée et limite les retards liés à la livraison. L’évaluation des capacités techniques, des antécédents en matière de qualité et des conditions tarifaires permet de minimiser les ajustements de dernière minute.
Gestion anticipée des chaînes logistiques
Une planification avancée du flux de composants baisse les coûts de stockage et évite les interruptions de montage. Un calendrier d’approvisionnement coordonné avec les sous-traitants permet d’obtenir les pièces au moment opportun. Par exemple, programmer la réception des systèmes hydrauliques 2 semaines avant leur intégration évite d’engorger les entrepôts. Le suivi informatisé du stock, via un logiciel ERP (Enterprise Resource Planning), garantit une disponibilité fiable et une visibilité sur les quantités, les délais et les coûts, estimés entre 50 000 et 100 000 EUR par an en logiciels et maintenance.
Mise en place d’indicateurs précis de suivi budgétaire
Des indicateurs chiffrés, tels que le coût unitaire par module, la marge de maintenance sur 5 ans, ou le taux de défaut par lot, permettent un pilotage strict. Un suivi mensuel des dépenses, avec un tableau de bord incluant une marge d’erreur de moins de 5 %, signale rapidement une hausse anormale des coûts. Grâce à des données consolidées, la direction identifie les écarts et ajuste le plan d’approvisionnement, assurant une stabilité du budget global.
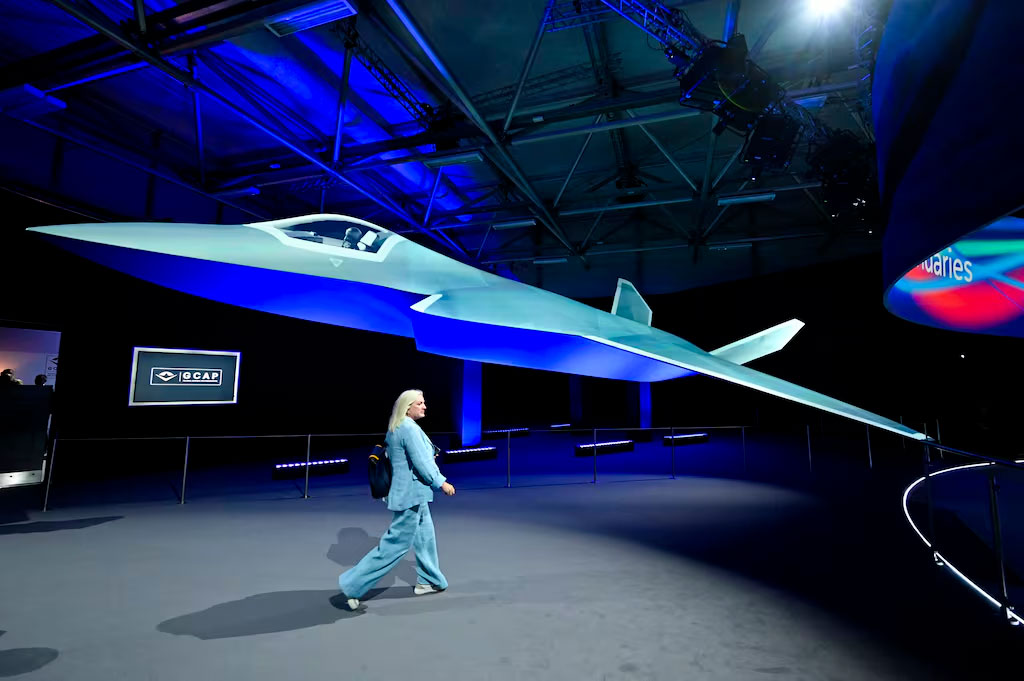
Perspectives et voies d’amélioration continues
Adaptation aux changements technologiques
La veille technologique constante permet d’anticiper l’intégration de composants plus performants et moins chers. Par exemple, un capteur radar d’une valeur de 150 000 EUR bénéficiant d’une miniaturisation récente améliore la précision sans accroître le coût total. Suivre les avancées dans les matériaux, l’électronique et la propulsion favorise une mise à jour régulière des options disponibles.
Formation des équipes et développement de compétences internes
Une mise à niveau des compétences internes via des formations techniques permet d’anticiper les besoins futurs. Par exemple, un technicien formé à la soudure laser sur alliage réduit le recours à un prestataire externe, économisant près de 40 000 EUR sur un cycle de maintenance. Des plans de formation ciblés, facturés entre 10 000 et 20 000 EUR par session, créent une réserve de savoir-faire directement disponible sur site.
Mesures incitatives favorisant l’innovation et la rentabilité
Des contrats flexibles avec des partenaires encouragent la recherche de solutions plus économiques. Un bonus de 5 % accordé à un fournisseur qui livre une pièce 10 % moins coûteuse incite à l’innovation. Cette approche suscite la proposition de technologies nouvelles ou de méthodes de production plus efficaces, limitant l’augmentation des coûts à long terme et stabilisant le budget global.
Avion-Chasse.fr est un site d’information indépendant.