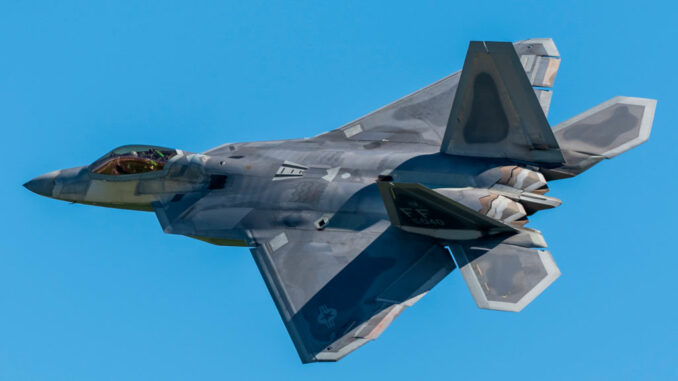
Les matériaux composites ont bouleversé la conception des avions de chasse. Détail technique et retour sur leur influence industrielle et militaire.
Les matériaux composites ont modifié la conception des avions de chasse depuis les années 1970. Leur utilisation ne résulte pas d’un effet de mode mais d’une nécessité technique. Les contraintes aérodynamiques, les coûts de maintenance, les besoins de furtivité et la pression sur les performances opérationnelles ont poussé l’industrie à abandonner une partie du métal. L’alliage d’aluminium, autrefois central dans l’aéronautique militaire, ne répond plus aux besoins des avions de combat modernes. Les polymères renforcés de fibres de carbone, les composites à matrice céramique ou thermoplastique sont désormais présents dans les cellules, les ailes, les entrées d’air ou les gouvernes. Le secteur ne s’est pas adapté par choix, mais par obligation industrielle. Les coûts initiaux sont élevés, mais les gains opérationnels et tactiques compensent. Cette évolution des matériaux a un impact direct sur la doctrine d’emploi et les chaînes de production aéronautique militaire.
Les matériaux composites dans la structure des avions de chasse
La montée en puissance des matériaux composites s’explique d’abord par leur densité. Le carbone-époxy présente une masse volumique moyenne de 1,6 g/cm³, contre 2,7 g/cm³ pour l’aluminium et 4,5 g/cm³ pour le titane. Le gain de masse atteint parfois 20 à 25 % sur certaines cellules. Ce différentiel améliore directement le rapport poussée/poids et la capacité d’emport.
Le Lockheed Martin F-22 Raptor incorpore environ 24 % de composites dans sa cellule, notamment pour les gouvernes, les bords d’attaque et la dérive. Le Dassault Rafale monte à 70 % de matériaux composites sur ses surfaces exposées, avec un gain de masse de 500 kg par rapport à une structure tout-métal. Cela permet de compenser le poids des systèmes électroniques et armements modulaires, sans sacrifier l’autonomie.
La production en composites exige des procédés industriels lourds : autoclaves à haute pression, découpe laser, assemblages par collage structural, et contrôle non destructif par ultrasons. Une cellule composite nécessite plus de temps d’usinage mais réduit les besoins en rivetage et soudures. Le F-35 Lightning II illustre bien cela : malgré des temps d’assemblage longs, la maintenance est simplifiée par des panneaux monoblocs remplaçables.
Le coût du kilogramme de fibre de carbone tissée oscille entre 40 € et 70 €, selon la qualité et le tissage. Le coût de production est supérieur à l’aluminium, mais le cycle de vie est allongé, et les inspections sont moins fréquentes. Les armées acceptent ce surcoût car il réduit les indisponibilités opérationnelles.
La fabrication additive en matériaux composites progresse également. Les pièces secondaires ou conduits internes peuvent être fabriqués en dépôt de fil fondu (FDM) ou frittage laser avec des charges en carbone ou kevlar. Ces procédés réduisent les délais de maintenance sur base avancée.
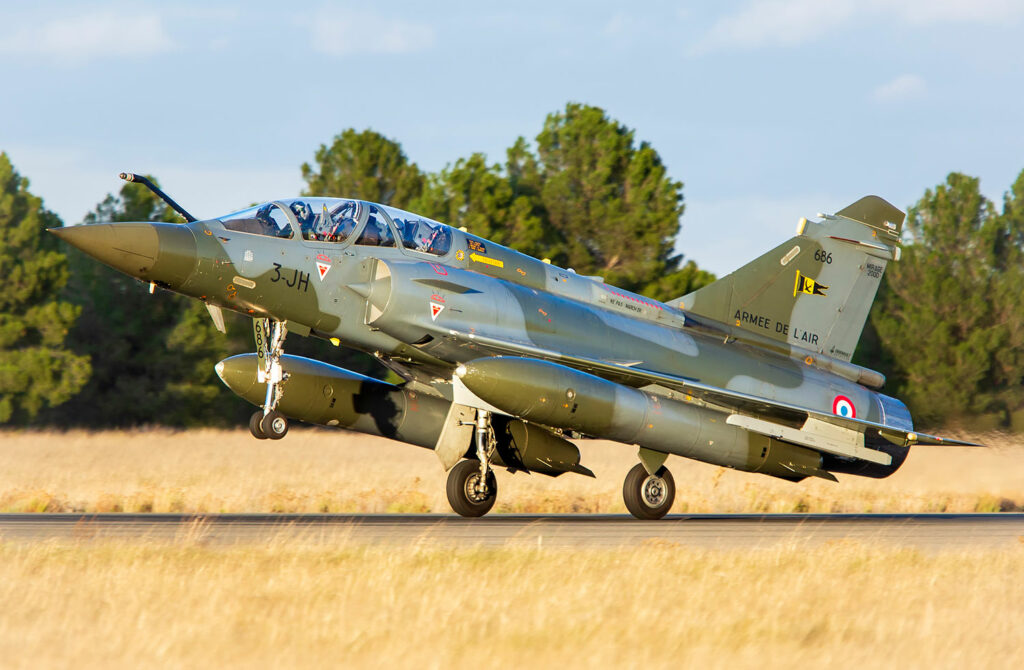
L’impact des composites sur la furtivité et les performances opérationnelles
Les avions de combat de cinquième génération ne peuvent plus se passer des matériaux composites, non seulement pour la masse, mais pour les signatures radar. Les surfaces composites intègrent des résines à absorption radar (Radar Absorbent Materials – RAM). Ces revêtements permettent d’abaisser la surface équivalente radar (SER) de plusieurs ordres de grandeur.
Le F-35 présente une SER inférieure à 0,005 m², contre 1 à 3 m² pour un chasseur métallique classique de quatrième génération. Cette réduction est en grande partie permise par des matériaux absorbants intégrés dans les composites de revêtement, évitant les angles droits et multipliant les formes courbes absorbantes.
Le Sukhoï Su-57, bien que plus modeste dans son usage de composites (environ 25 % de la cellule), intègre également des polymères absorbants dans ses entrées d’air et dérives. La Chine, avec le Chengdu J-20, pousse plus loin l’intégration de RAM dans une structure composite évaluée à 40 %.
Ces choix ont des conséquences opérationnelles directes. Un avion avec une SER réduite peut engager ou se repositionner sans être détecté. Cela modifie les doctrines de pénétration en profondeur, d’appui électronique et de supériorité aérienne.
Cependant, la contrainte technique reste forte. Les surfaces RAM sont sensibles à l’abrasion, à l’humidité et nécessitent des réparations spécifiques. Chaque impact sur une structure composite peut nécessiter une dépose complète du panneau pour contrôle, contrairement aux tôles métalliques réparables localement.
Enfin, les composites modifient les régimes thermiques des avions. Le coefficient de dilatation thermique est très faible, mais les transferts de chaleur sont moindres que dans le métal. Cela nécessite des systèmes de gestion thermique indépendants pour les baies électroniques et les armements internes.
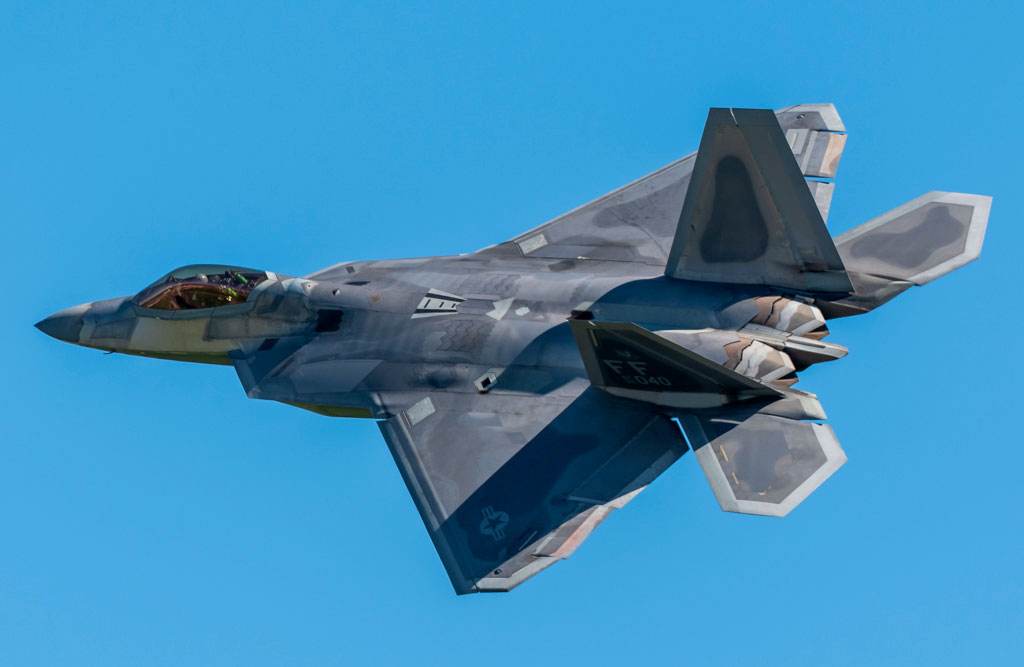
L’influence sur la chaîne industrielle et la doctrine d’emploi des chasseurs
L’introduction des matériaux composites bouleverse toute la chaîne industrielle aéronautique. Les centres de production traditionnels, équipés pour le fraisage aluminium, sont dépassés. La fabrication composite repose sur la pose robotisée de fibres, le drapage automatisé, et des cycles de polymérisation longs, avec temps de cycle moyen de 6 à 12 heures par pièce.
Le F-35 a nécessité la construction d’une ligne spécifique de drapage automatisé dans les usines de Lockheed Martin. Chez Dassault, le Rafale a obligé à restructurer la ligne de Mérignac pour intégrer les procédés de collage et durcissement. L’investissement initial dépasse souvent 300 à 500 millions € pour une ligne composite complète.
La logistique évolue également. Les pièces ne peuvent plus être stockées comme des composants métalliques. Le stockage exige des environnements climatisés, surtout pour les résines non polymérisées.
Du point de vue opérationnel, cela implique une réduction des équipes de réparation de terrain, mais une augmentation des techniciens spécialisés. La maintenance devient plus spécialisée, moins improvisée. Certaines armées peinent à maintenir ce niveau de technicité dans des contextes expéditionnaires.
L’utilisation de matériaux composites impose aussi de nouvelles normes OTAN de certification. La résistance au choc balistique, l’échauffement en vol supersonique ou les contraintes en catapultage (pour les avions embarqués) doivent être recalculés selon d’autres matrices de fatigue que celles de l’aluminium.
Le recours aux composites permet cependant de standardiser certaines pièces sur plusieurs plateformes. Le Rafale, le nEUROn et le Falcon 10X partagent certaines technologies de drapage, de collage et d’assemblage. Cette mutualisation réduit les coûts et facilite les développements croisés entre aviation civile et militaire.
Avion-Chasse.fr est un site d’information indépendant.